6 Strategies for Shaping Weighing Processes and Reducing Downtime
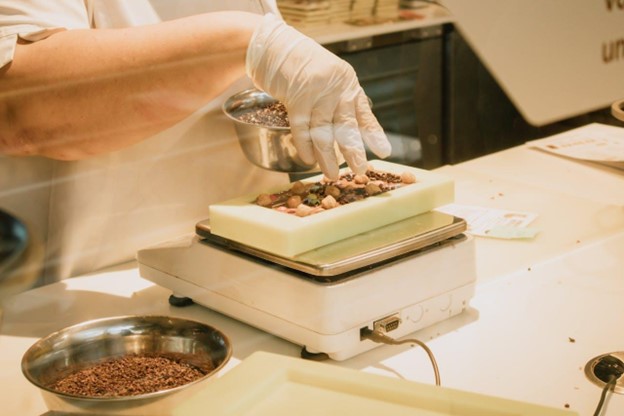
Efficient weighing processes are crucial for maintaining a smooth workflow. In industries like manufacturing and logistics, precise weight measurements are essential for maintaining quality control, meeting regulatory standards, and optimizing supply chain operations.
A small error in weighing can lead to significant issues, from production delays to financial losses. For example, in the agriculture sector, precise weight measurements are critical for livestock management and feed distribution.
Explore the following strategies to set the stage for minimizing downtime while ensuring accuracy and reliability in your weighing operations.
Leverage Technological Advancements
Modern weighing scales come equipped with digital interfaces and automated systems that reduce human error and improve measurement precision. For instance, automated calibration features ensure consistent accuracy, minimizing the need for manual adjustments.
In addition to automated systems, integrating weighing processes with other digital tools, such as enterprise resource planning (ERP) systems, can streamline data management. This integration allows for real-time data tracking and analysis, enabling better decision-making and process optimization.
Use Industrial Scales
Industrial Weighing Scales are designed to handle the demanding requirements of various industries, making them indispensable for streamlining weighing processes. These scales offer robust construction, high precision, and durability, ensuring reliable performance even in harsh environments.
For example, industrial scales used in the logistics sector can withstand heavy loads and frequent use, reducing the risk of equipment failure. Additionally, industrial scales often come with customizable features, allowing businesses to tailor them to their specific needs.
Preventive Maintenance Practices
Regular maintenance checks can identify potential issues before they escalate into major problems, reducing downtime and extending the lifespan of your equipment. For instance, routine calibration and inspection of load cells, sensors, and other critical components ensure consistent accuracy and reliability.
One specific area of preventive maintenance is livestock scale servicing. In the agriculture industry, livestock scales are essential for managing animal weights and feed distribution. Regular servicing of these scales ensures accurate weight measurements, supporting efficient livestock management practices.
Enhance Process Automation
Automated weighing systems can handle repetitive tasks with precision and consistency, freeing up your staff to focus on more complex responsibilities. For instance, automated conveyor systems integrated with weighing scales can efficiently handle bulk materials, reducing the need for manual handling.
Additionally, automation reduces the risk of human error, enhancing measurement accuracy and consistency. Implementing automated weighing processes not only improves efficiency but also enhances workplace safety by minimizing the need for manual lifting and handling.
Customize Weighing Solutions
Customizing your weighing solutions to align with your specific requirements is essential for optimizing your operations. Whether it’s selecting the right type of equipment or integrating it with your existing systems, customization ensures that your solutions are tailored to your unique workflows.
Working with experienced solution providers can help you identify the best options for your business. They can offer expert advice on equipment selection, system integration, and maintenance practices, ensuring that your weighing processes are efficient and reliable.
Implement Quality Control Measures
Quality control is a critical aspect of efficient weighing processes. Implementing robust quality control measures ensures that your weighing operations meet industry standards and regulatory requirements.
For example, establishing standard operating procedures (SOPs) for processes can enhance consistency and accuracy. Regular audits and inspections of your equipment and processes further reinforce quality control.